Q: Matt – great to be speaking with you today. To get us started, could you share with us some details on your background?
A: Sure! Most of my early career focused on system level and electrical design of robots and automated industrial equipment. I had some really great mentors that taught me everything from motor control to nuanced circuit board design, and feel like I’ve been in the weeds of every aspect of robot design. About 10 years ago, my career focus shifted to leadership, what makes a great place to work, what makes a great team, and how to drive constant improvement.
Q: How did you get into the field of robotics?
A: Honestly, random luck! I followed my girlfriend (now wife) to Austin after my junior year at BU, and landed an internship for a company that made custom automation for AMD. I immediately fell in love! We solved practical problems, and that suits me – I’m practical. And writing software that resulted in robot motion, whether right or wrong, was really fun! The founders were an extraordinary group of people, which I really only understood much later in my career. They were empowering and selfless, I learned so much from them.
A few years into that first job, I became a sort of electrical-engineering apprentice working for one of the founders. I spent about 7 years building system level and board design skills. I later took those skills to Brooks Automation where I spent 13 years, culminating in the development of what I think is still probably the best multi-axis control system ever created. Again, I was fortunate to work with a group of brilliant engineers, it was amazing to see what we were capable of designing. As my responsibilities grew, I learned how to build capable teams and the fundamentals of what is required to have consistently successful development projects. In 2016, I helped launch Alert Innovation, a company developing grocery order fulfillment automation, as well as a great company culture. I was excited to take what I learned there and apply it to Realtime Robotics earlier this year – we are committed to making an exceptional company!
Q: What are your responsibilities at Realtime Robotics?
A: At Realtime, I’m the VP of Engineering. My first priority is making sure engineering runs well – that we have the skills necessary to realize the product vision, that we deliver on time and with the expected quality. A lot of my job involves listening to understand our challenges and building consensus to drive changes that move us forward. We’re already working to empower engineers and leaders, build our technical and leadership skills, clarify responsibilities and technical objectives, and hire missing links in our organization.
Q: Why do you believe culture is so important to a company’s success?
A: I believe most everyone wants to have a job where they can have impact, where they can do their best work. Our team needs a leadership team that supports them, a place where the big problems flow to the top, not the reverse. The leadership team steers a path that provides clear objectives that are achievable and will ultimately make the company successful. We’re working to build a trusting environment where everyone feels safe to ask questions or raise their hand when they need help. When people feel like they’re genuinely supported, their skills align well with their work, and their management team understands and supports their career goals, performance benefits.
Q: What excites you about the future of Realtime Robotics?
A: I truly believe Realtime has a great future ahead of it. The company is solving an important industry problem with no legitimate competitors, and has already gathered a lot of attention from potential customers with early drafts of the product. The path to broad industry acceptance is relatively straight forward.
Q: What excites you about getting out of bed in the morning?
A: I love problem solving. Having a challenge in front of me and working out how to meet that challenge, solve that issue, overcome that obstacle and succeed. I’m drawn to the task of understanding a problem, learning why previous solution attempts may have failed, and finding the answer. That is what drives me on a daily basis.
Q: What do you like to do when outside of work?
A: I’m told that I’m a workaholic in some ways, but when you love what you do it’s tough to put it down. I have a fantastic wife and three great kids (no engineers somehow?) on the cusp of leaving home, so we’re cherishing our last years with them. I am definitely a DIY person, I maintain our cars, take on home construction projects (not all successfully), and am attempting a garden. I love astronomy, good cookies, road bike riding, hiking, meals with family, camping, ping-pong, and travelling to foreign countries.
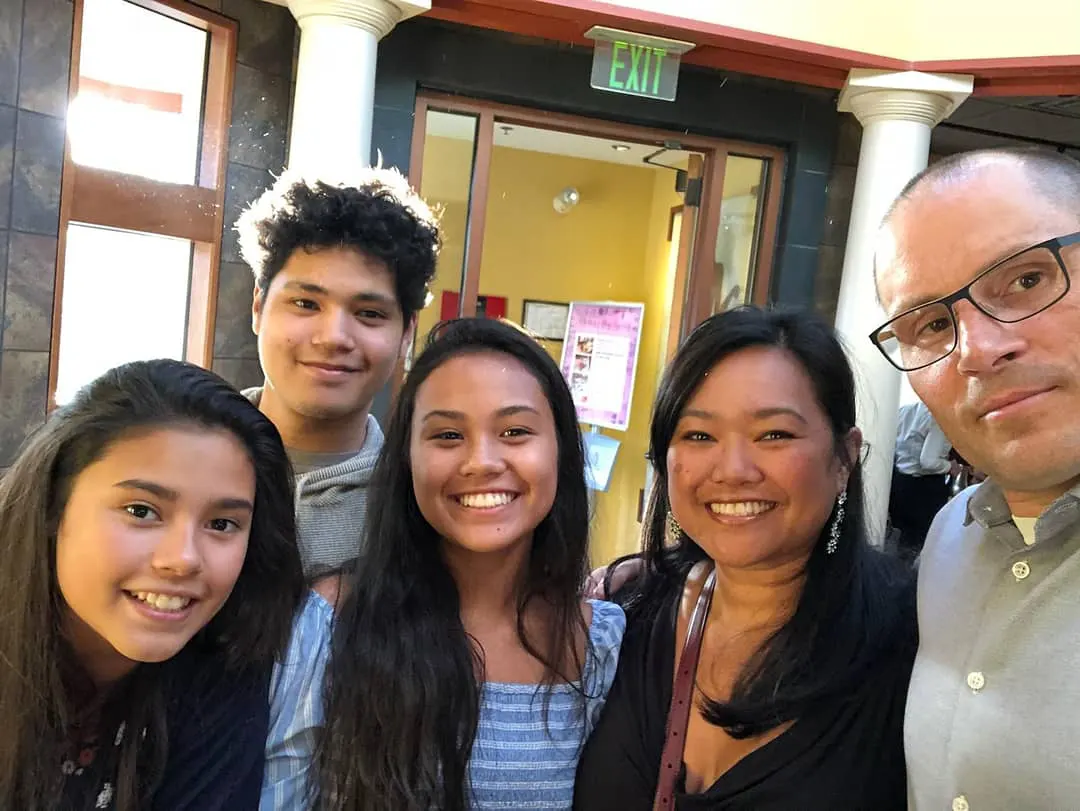
Q: What advice would you like to impart on our readers? Any piece of terrific advice you’ve received along the way?
A: Performance follows passion. People make miracles happen when they’re excited about what they do. I encourage students and young employees to experiment early, try and figure out what you love before life locks you into a job. Don’t settle!